What causes the most common errors of radar level sensor
Huachuang measurement and control Huachuang measurement and Control Technology Co., Ltd 2023-04-21 14:41
In the liquid level measurement industry, radar level gauges have become the first choice for users to consider. This is because the radar level gauge has a wider range of applications than other measuring instruments, and has more advantages in installation and use. Of course, any product will have its own shortcomings. In fact, the radar level gauge still has many problems that need to be improved. Through the gradual improvement of our technical level, we are gradually improving. So, let us take a look at the usual errors in radar level gauges? This is how the technicians who have been dealing with mine level gauges for a long time introduced to me.
Under normal circumstances, the error of the radar level gauge is mainly due to the error in the installation of the instrument, which will cause the echo signal to be interfered and cause measurement errors. For this reason, experts reminded that, during installation, the height of the tank and the size of the beam angle must be taken into account, and sufficient installation space should be reserved for the radar level gauge.
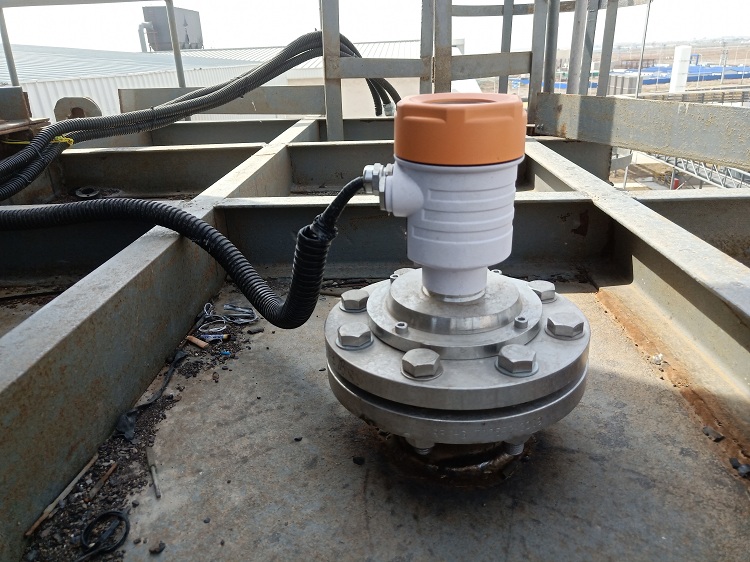
In addition, the following common errors will occur:
1: Measuring dead zone: The output of the radar level gauge is 4-20mA current during the measurement. Due to the measured liquid itself and the probe, there are two dead zones in its measurement, namely the upper dead zone and the lower dead zone. . The minimum distance that can be measured between the upper dead zone liquid level and the upper reference point is about 0.1m~0.5m; the lower dead zone is at the bottom of the probe. As the real liquid level in the tank changes, the measurement result is not Part of the change.
2: Error caused by the measured liquid: When measuring the interface, the dielectric constant of the upper liquid must be 10 greater than the dielectric constant of the lower liquid level. If the dielectric constant of the two interfaces is not much different, it will become a wave pattern. During the measurement, since the time used for the liquid level and the interface level is basically the same, the two returned signals will overlap and affect the measurement result.
3: The viscosity of the measured liquid is too large: the liquid has a high viscosity. Such a liquid is likely to adhere to the probe, which will affect the signal transmission and cause errors in the measurement; if the viscosity is greater, the medium will be connected to the probe. Together, the probe must be cleaned regularly at this time.
4: The error caused by the radar level gauge itself: The radar level gauge uses radar technology, and most of the errors are caused by on-site installation.
In order to effectively avoid these possible problems, when installing the radar liquid level timing, the matters that should be paid attention to:
1. When installing the radar liquid level timer, the feed inlet, the feed curtain and the vortex should be avoided, because when the liquid is injected, it will produce a false echo whose amplitude is much larger than the effective echo reflected by the measured liquid level. At the same time, the irregular liquid level caused by the vortex will scatter the microwave signal and cause the attenuation of the effective signal, so they should be avoided;
2. For containers with agitator, the installation position of the radar level gauge should not be near the agitator, because irregular vortices will be generated during mixing, which will cause the attenuation of the radar signal. At the same time, the blades of the stirrer will also cause false echoes to the microwave signal, especially when the relative permittivity of the measured object is small and the liquid level is low, the influence caused by the stirrer is more serious;
3. When the radar level gauge is used to measure the level of corrosive and crystalline objects, in order to prevent the influence of the medium on the sensor, the manufacturer generally adopts a structure with a PTFE measuring window and a separation flange. The temperature of these parts can not be too high, the maximum temperature of PTFE is 200 ℃. In order to avoid the influence of high temperature on the radar antenna, and to prevent the presence of crystals on the diaphragm from affecting the normal operation of the instrument, a safety distance of at least 100-800mm between the flange end face and the highest liquid level is required.